Så tillverkas storsäljaren Nissan Qashqai: ”En emotionell bil”
Japan har lyckats få fram en och annan framgångsrik biltillverkare. Nissan är en av många men varför ligger en av deras fabriker i Sunderland? Och hur byggs den uppdaterade Nissan Qashqai? Vi lägger i Högsta Växeln för att besöka fabriken på den brittiska östkusten.
Japanska bilar har gjort sig kända för sin höga byggkvalitet och tillförlitlighet. Dock har Japan, ur ett europeiskt perspektiv, en lite problematisk geografisk placering – på andra sidan jorden.
Det gör att man kan riskera att få leveranstider som inte är särskilt tillfredställande samtidigt som fraktpriser och importtullar driver upp priserna.
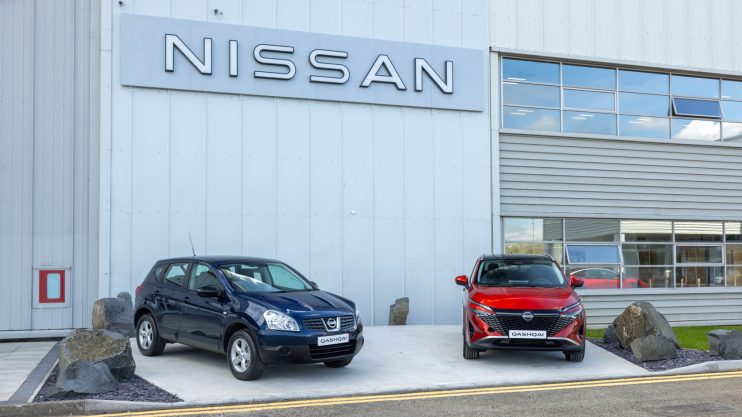
Foto: Nissan
I Europa för Europa
Det här är en av de bakomliggande orsakerna till att Nissan bestämde sig för att öppna en fabrik i Europa i mitten av 80-talet. Genom att ha en egen fabrik i Europa kunde man leverera flera modeller betydligt snabbare än tidigare.
Samtidigt kom man på att de europeiska kunderna var närmare och på så sätt skulle man kunna utveckla produkter som passar de europeiska kunderna bättre.
Platsen för fabriken blev Sunderland i norra England och år 1986 började ”Nissan Motor Manufacturing UK Ltd” slutmontera Bluebirds som levererades som byggsatser från Japan.
I rask takt expanderade fabriken och numera är den på många sätt väldigt europeisk. Råmaterial och komponenter från underleverantörer köps till absolut majoritet från närområdet.
Den storsäljande modellen Qashqai designades till stor del i Europa för den europeiska marknaden.
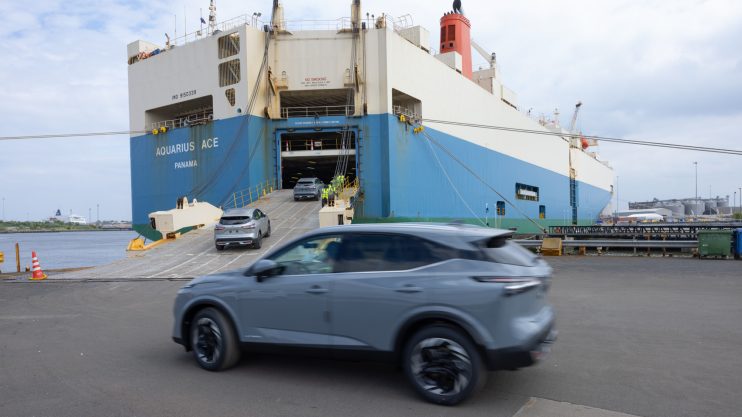
Riskerade stängning på grund av Brexit
Trots att fabriken befäst sig som en hörnsten i Nissans globala strategi var dess överlevnad osäker under år 2020 på grund av Brexit.
Tack vare att förhandlingarna mellan Storbritannien och Europa föll väl ut flyttade inte fabriken till det europeiska fastlandet.
Tur är väl det, framför allt för den brittiska lokalbefolkningen, eftersom fabriken faktiskt är den största i Storbritannien när det gäller produktion av bilar.
Över 6 000 personer är anställda på fabriken och underleverantörer i närområdet genererar mångdubbelt fler arbetstillfällen.
Efter att debaclet med Brexit var avklarat har Sunderland-fabriken befäst sin position och med EV36Zero-visionen spelar Sunderland en nyckelroll.
Målet med EV36Zero innefattar att omvandla Nissan Sunderland till en produktionshubb för elbilar, där strategier för förnybar energi och batteriproduktion samlas och utgör en modell för framtidens bilindustri.
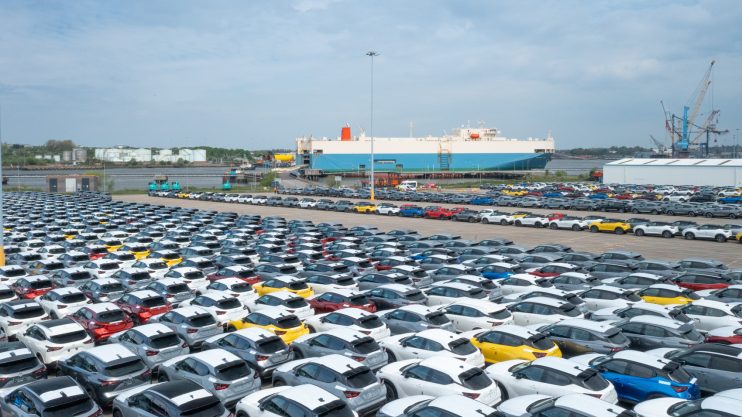
Föregångsfabrik
Projektets vision är bland annat en ny eldriven crossover för produktion i Sunderland, en giga-batterifabrik tillsammans med Envision-AESC och en utbyggnad av fabrikens mikronät med förnybar energi.
Det här passar fabriken bra då den redan har en stark hållbarhetsprofil tack vare sitt eget elnät som bland annat består av flera vindturbiner. I dagsläget kommer 20 procent av det totala energibehovet från egenproducerad el, resten köps in.
Målet är dock att utöka den här siffran framöver och man håller bland annat på att byta ut turbinbladen för att öka det möjliga effektuttaget.
I dagsläget producerar dock fabriken bara två modeller, den senaste versionen av Nissan Qashqai och Juke.
Historiskt har dock elbilen Leaf rullat ur fabriksportarna men även Infiniti som är Nissans lyxigare varumärke har tillverkats i Sunderland. Men hur ser processen ut när en ny bil tar form i Sunderlandfabriken?
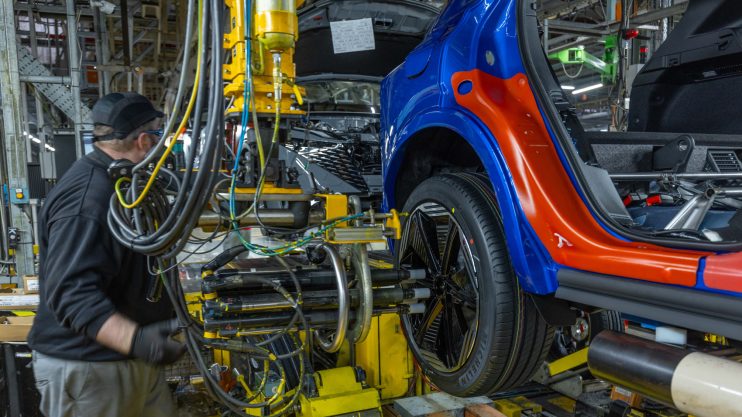
Pressverket
Produktionsprocessen börjar med att stora rullar av stål och aluminium stansas ut till en grundform matchande den karossdel som materialet sedan ska ta form till. Här märker man direkt av hållbarhetsfokuset eftersom allt restmaterial återvinns.
När det sedan finns en grundform transporteras den in i flera olika hydrauliska pressar som skapar karrospanelernas slutgiltiga form. Processen är fascinerande att se och kraften som pressarna formar plåtarna med är imponerande.
Det blir även väldigt tydligt hur omfattande förändringar som krävs för att uppnå minsta lilla förändring av karossformen. Nya formar behöver tas fram och dessutom behöver de gamla behållas i flera år för att kunna garantera reservdelsförsörjningen.
När plåtdelarna och panelerna antagit sin slutgiltiga form transporteras de till en annan hall där över 1 000 robotar svetsar och limmar ihop plåtdelarna.
I det här stadiet börjar bilens faktiska former bli urskiljbara. Qashqai består av 41 olika karosskomponenter varav 20 är i aluminium, vilket sparar cirka 60 kilogram men även bidrar till en mer korrosionsbeständig slutprodukt.


Luftdusch
Nästa steg är att applicera ett ytskikt som består av en korrosionsskyddande beläggning, grundfärg, färg med kulör och slutligen klarlack. I den delen av fabriken som applicerar ytskiktet rådde strikta riktlinjer för att få komma in, yttersta renlighet är nödvändig.
Besökarna draperades i skyddskläder och fick passera en luftdusch där även de minsta partiklarna skulle blåsas av kroppen.
När bilen lackeras låter man karossen vara elektriskt laddad på ett sådant sätt att den drar åt sig färgen vilket bidrar till att minimalt med färg går till spillo.
Sprutmålningen utförs helt av robotar men flera operatörer klädda i dräkter som hämtade från en science-fiction-film går omkring och kvalitetssäkrar arbetet.
Målningen av taket är ett av de mest kritiska momenten eftersom Qashqai kan fås i tvåfärgat-format och då genomförs maskeringen för hand.
När färgen torkat inleds monteringen av bilens interiör. I den här fasen av produktionen utrustas dörrarna med klädsel och elektronik. Dörrarna och dess elektronik ansluts dock i ett senare skede och följer därför bilen på en separat linje.’

Ingen elbilsproduktion
I Sunderland-fabriken bygger Nissan bilar med bensin-, hybrid- och elmotorer omväxlande. Eller det gjorde Nissan i alla fall när Leaf producerades här – tanken är att det åter ska bli så när nya elbilar introduceras.
I nästa steg förses fordonen med sin mekanik och drivlina. På en självkörande vagn levereras motorn, växellådan och fjädringen för att sedan giftas ihop med karossen.
Bilar med bensinmotor får 6 liter bränsle tankat innan en intensiv inspektion av varje fordon tar vid. Nästintill 1 000 olika punkter inspekteras och om något inte överensstämmer åtgärdas det direkt. Alla bilar tas sedan ut på en 1 mil lång testrunda.
I vissa fall körs istället en längre testrunda för att stickprovskontrollera att allting fungerar som det ska.
Nissan jobbar enligt Just-in-Time och bilarna lagras oftast bara fyra timmar innan de forslas vidare ut i Europa och världen. 20 procent av produktionen stannar i Storbritannien.

Framtiden är elektrisk
Som tidigare nämnt tillverkades bara två olika modeller i fabriken under besöket men fabriken förbereder sig för en framtid där den bara bygger elbilar.
Flera av förberedelserna är redan långt gångna och bland annat har en fabrik för montering av battericeller byggts upp. Flera modifikationer av fabriken är också på gång vilket de många elektrikerna och automationsingenjörerna skvallrade om.
På plats för att prata mer om framtiden fanns Francois Bailly, Region Chief Planning Officer. Innan slutet på 2026 kommer 16 nya elektrifierade bilar att lanseras samtidigt kommer 14 nya förbränningslaternativ att adderas för att komplettera produktportföljen.
Det här är dock de globala siffrorna och Europa kommer att få ta del av 6 nya modeller. Målet är att röra sig tillbaka till de historiska nivåerna där snittet de senaste 10 åren är 4,7 miljoner bilar medan man bara sålde 3,4 miljoner 2023. 2026 är målet att Nissan ska sälja 300 000 fler enheter än vad man gör just nu.

Nissan ska väcka känslor
Bailly lyfter fram Nissans förmåga att väcka känslor som en orsak att varumärket kommer att lyckas med sina mål.
”Bara Nissan, och jag utmanar vem som helst att hitta en annan OEM som kan göra den här typen av emotionella bilar” understryker Bailly.
Ur ett produktionstekniskt perspektiv lyfter den regionala produktionschefen Alan Johnson fram förmågan att producera fordon på ett effektivt sätt där man balanserar automation och mänsklig arbetskraft på ett effektivt sätt.
Han lyfter fram hur tyska tillverkare ibland kan investera i avancerad automation som inte är affärsmässigt vettig.
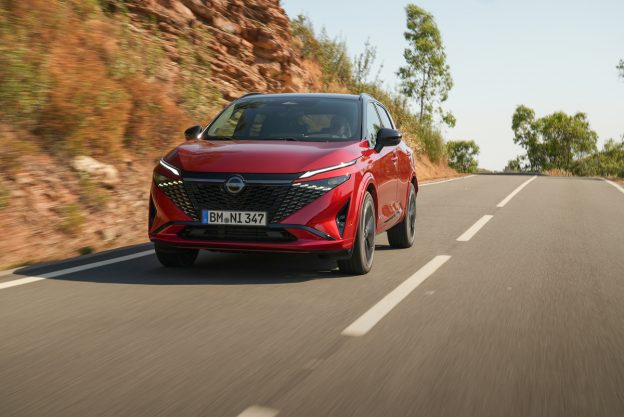
Ny version av storsäljaren
Men det var inte bara produktionsanläggningen och framtidsutsikterna som undersöktes under besöket i Sunderland utan vi fick även en möjlighet att utforska den ansiktslyfta Qashqai.
Qashqai är designad och utvecklad i Storbritannien med den europeiska marknaden i fokus. Den första Qashqai tillverkades vid fabriken i Sunderland i slutet av 2006 och är den mest tillverkade modellen i Storbritanniens historia. Det är med andra ord en modell som har ett arv att leva upp till.
Estetiken är kraftigt moderniserad och tar mycket inspiration från elbilen Ariya. Uppdateringen är i mitt tycke lyckad och estetiken känns mer unik och premiumbetonad.
Interiört finner man i stort sett samma inredning som i X-Trail. Materialvalen känns robusta och balansen mellan fysiska knappar och digitala instrument är väl avvägd. Priserna startar från 319 000 kronor.
För Qashqais del finns goda möjligheter att fortsätta att vara en storsäljare och för Sunderland-fabriken ser framtiden ljus ut.
Det gäller bara att Bailly har rätt och att Nissan lyckas framkalla tillräckligt mycket känslor så att försäljningen återgår till var den en gång var.
Otvetydigt är dock att fabriken står väl rustad för framtidens utmaningar och varumärkets transparens kring produktionen inger ett solitt förtroende.