Så garanterar Audi att deras elbilar är bra för miljön – på riktigt
När man nämner bilproduktion och Belgien lär de flesta svenskarna föra tankarna åt Volvos fabrik i Gent. Men faktum är att Belgien, trots avsaknaden av ett inhemskt varumärke, kan stoltsera med ytterligare en fabrik, där Audi nu bygger sina elbilar.
Den första stenen till fabriken lades 1 september 1948 vilket innebär att det har producerats bilar av olika varumärken i Bryssel under mer än 70 år.
Vi lade i Högsta Växeln och begav oss till Belgien för en rundtur.
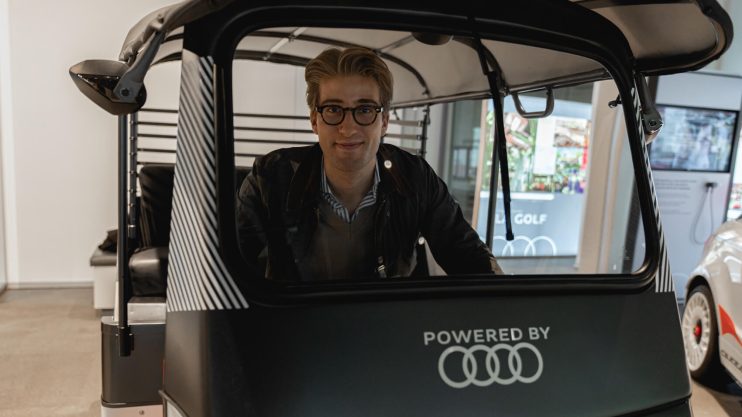
Ett familjeföretag från grunden
Fabriken som ligger centralt placerad drygt en halvmil från EU-parlamentet i Bryssel leder utvecklingen av Audis hållbara produktion.
Med netto-noll CO2-utsläpp sedan ett antal år är bilarna som produceras där några av de mest hållbara som går att köpa.
Men så har det inte alltid varit, utan fabriken har fått anpassa sig efter rådande trender och förändringar. Pierre D’Ieteren, som var arvinge till en familj av industrialister, tog initiativ till att starta fabriken.
D’Ieteren SA som familjeföretaget heter hade varit en stor importör av amerikanska bilar under åren före krigsutbrottet och slöt kort efter krigsslutet ett avtal för att starta produktion av Studebaker lokalt i Belgien.
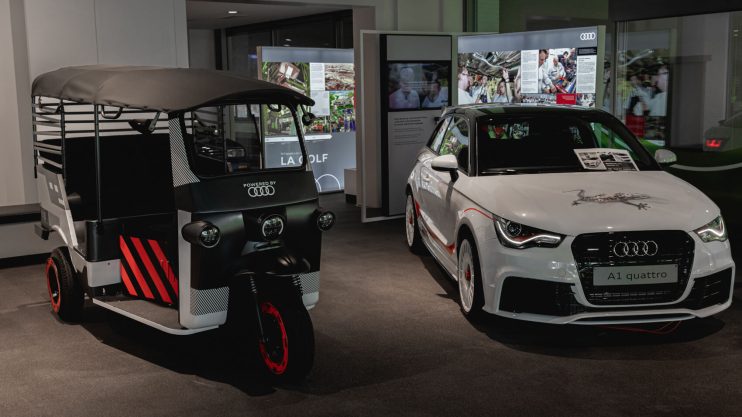
Med amerikanska influenser
Tack vare partnerskapet mellan D’Ieteren och Studebaker blev det den tredje mest populära amerikanska bilen i Belgien, efter Ford och Chevrolet.
Kort efter avtalet med Studebaker slöt man även ett avtal om att producera åt Volkswagen.
När bilindustrin återhämtade sig efter kriget blev det uppenbart att Belgien och övriga Europa hade ett fokus på mindre bilar jämfört med de som var avsedda för Nordamerika.
1954 började anläggningen montera Volkswagen-bilar vid sidan av Studebakers.
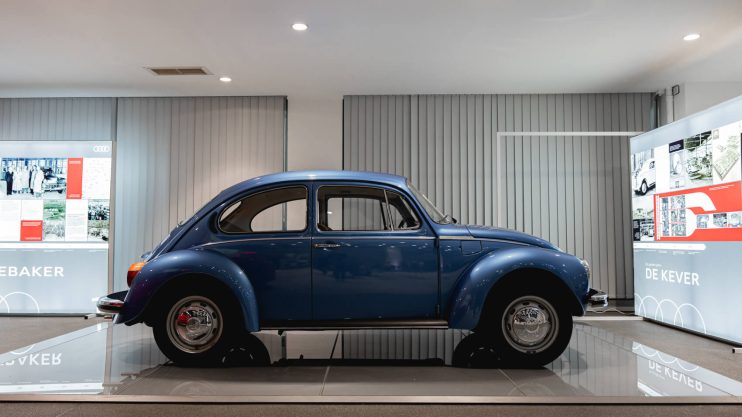
Porsche – made in Brussels
För D’Ieteren SA var det här tursamt då Studebaker drog sig tillbaka från den europeiska marknaden sex år senare på grund av finansiella problem.
Produktionsanläggningen i Bryssel koncentrerade sig från och med nu på att bygga Volkswagen och Porsche.
Bilar som Volkswagen Karmann Ghia och Porsche 356 har producerats där. 1970 tog Volkswagen över fabriken från familjen D’Ieteren och på den vägen har den hamnat i Audis ägor.
Idag tillverkar anläggningen Q8 e-tron och Q8 e-tron Sportback. Det här är Audi:s elektriska flaggskepp vid sidan om e-tron GT och det är därför vi begett oss till Bryssel.
Vi ska få ta del av den fascinerande processen när tusentals komponenter och plåt förvandlas till en av de mest kompetenta elbilarna på marknaden.
Ur fabriken i Bryssel rullar det ut en ny bil per 90:e sekund och förser alla marknader utom den kinesiska med de två elektriska suv-modellerna.

Audi genomförde en stor ombyggnation
Inför att de elektriska modellerna skulle börja produceras genomfördes en omfattande ombyggnation samtidigt som produktionen fortfarande pågick.
Det var A1 som var den modellen som senast tillverkades i fabriken bortsett från de elektrifierade suvarna.
200 000 timmar av utbildning hade redan genomförts innan produktionen startade. Bland annat var man tvungen att lära ut hantering av högspänningselektronik vilket Bryssel-fabriken inte hanterat tidigare.
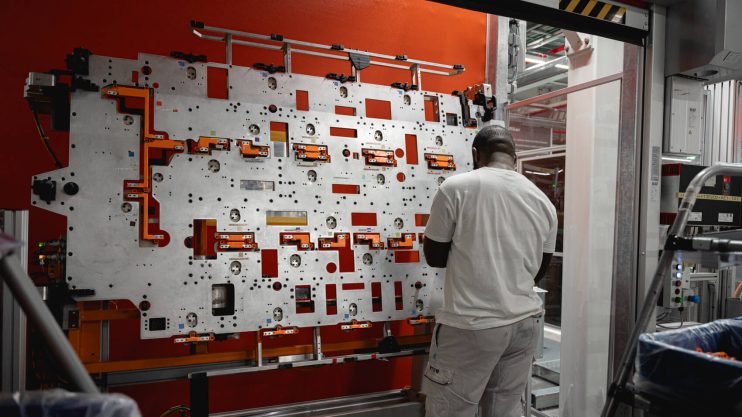
Karossverkstaden
Bilen börjar sitt liv i karossverkstaden där färdiga stål- och aluminiumplåtar, cirka 300 stycken, kommer med tåg från Neckarslum och Ingolstadt.
Arbetet utförs av 600 robotar och 400 anställda. I karossverkstaden svetsar man även ihop batterifacket som har separata platser till varje battericell. Karossverkstaden är i stort sett helt automatiserad.
Det är i karossverkstaden man lägger grunden för en bil med korrekta panelgap och god passform och varje kaross 3D-skannas för att analyseras digitalt.
Sedan ytbehandlas bilen i fyra olika lager. Korrosionsskydd, basfärg, kulör och klarlack genererar tillsammans ett 0,12 millimeter tjockt lager.
Samtidigt som karossen svetsas ihop monteras drivlinan och chassit ihop i en annan del av fabriken.
Självkörande små transportbilar ser till att de olika komponenterna som batteripaketet, motorerna och hjulupphängningarna med stötdämpare kommer till rätt plats vid rätt tidpunkt.
Först monteras fram- och bakaxlarna till elmotorerna som sedan monteras i fram- respektive bakhjulsupphängningarna. Slutligen monteras batteriet.

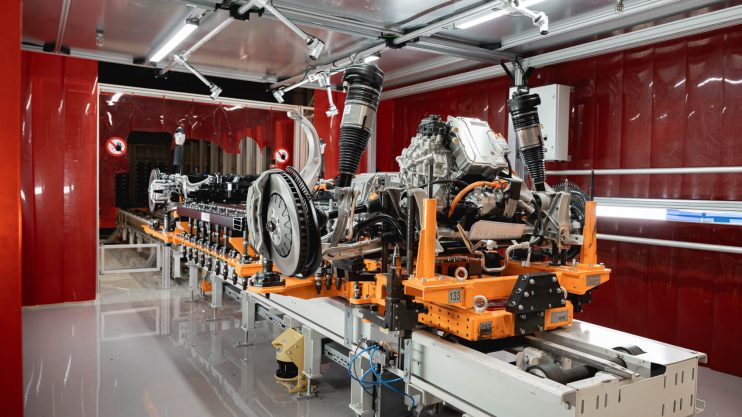
Lokalt monterat batteripaket
Innan batteripaketet monteras ihop med resterande komponenter har det monterats ihop i en nybyggd del av fabriken.
Batterifacket kommer in i ena änden och ut i den andra kommer ett fullt funktionellt batteripaket. Först fylls de 46 facken med värmeledande skum för att sedan få de enskilda cellerna monterade på varsin plats.
Trots att en stor andel av arbetet är automatiserad spelar fortfarande människorna en stor roll, kabelstammen monteras exempelvis manuellt. Mycket engagemang och fokus läggs ner på att kvalitetssäkra batteripaketet så att det möter de hårt ställda kraven.
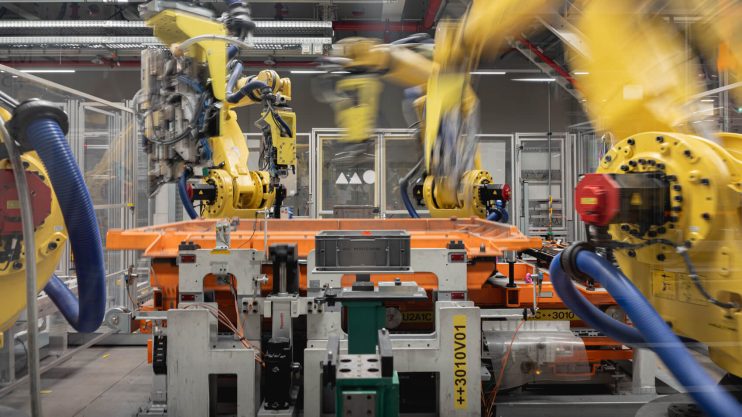
Giftemål på horisonten
Sedan är det dags att gifta ihop karossen med drivlinan, hjulupphängningarna och batteripaketet. Processen är helt automatiserad och bilen fortsätter nu sin färd på andra våningen.
Rent teoretiskt skulle man nog med hjälp av en monterad ratt, pedalställ och fälgar kunna framföra bilen, alltjämt på ett inte särskilt trevligt sätt.
Därför fortsätter bilen sin färd längs monteringslinan och får säten, stötfångare, ljudisolering med mera monterat.
Slutmonteringen är den del i fabriken som har flest anställda, 1 000 stycken, och har arbetsmoment som är svåra att automatisera. Totalt monteras cirka 4 000 olika delar längs monteringslinjen som sträcker sig över en kilometer.
Innan bilen rullar av linan testas elsystemet. E-tron-modellerna innehåller 175 stycken elektroniska kontrollenheter jämfört med bara 31 i Audi A1 som tidigare byggdes där.
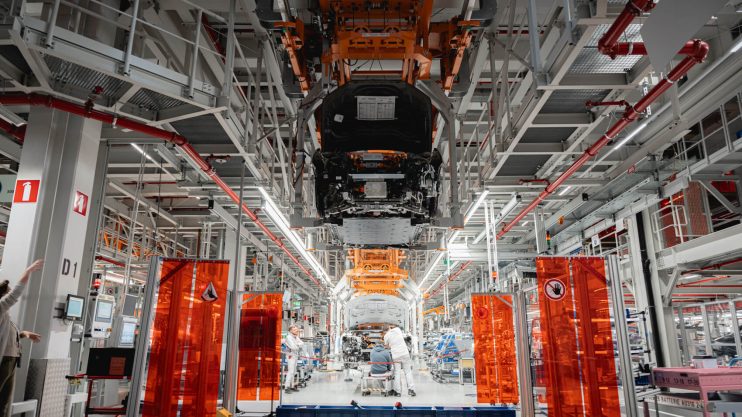

Audi har hållbarhet i fokus
Än så länge är det inga dramatiska skillnader från hur det brukar se ut i en bilfabrik så vad är det då som gör att fabriken i Bryssel är så otroligt mycket mer hållbar ur ett miljöperspektiv?
Det mest uppenbara när man tittar på fabriken utifrån är närheten till järnvägsområdet och de stora mängderna med solcellspaneler som täcker stora delar av fabriken. Ytan som är täckt med solceller täcker motsvarande 16 fotbollsplaner.
Den omfattande mängden solceller gör att fabriken kan försörja sig med sin egen el till cirka 31 procent eller motsvarande den energimängd som 2 500 hushåll förbrukar per år.
Man sparar även motsvarande 3,5 gWh per år genom att ha optimerat uppvärmningen av fabriken. En stor del av optimeringen bygger på att man återanvänder restvärme på ett så effektivt sätt som möjligt.
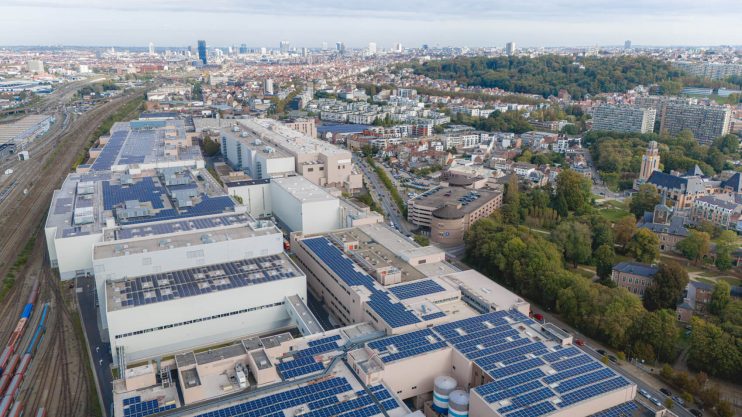
11 000 ekträd
Men man har också valt att arbeta med mer okonventionella sätt för att bidra till miljön. Bland annat så har varje Audi-fabrik ett ekträds-projekt och så är fallet för Bryssel-fabriken också. För några år sedan planterades 11 000 ekträd söder om staden.
För att spara ytterligare koldioxidutsläpp så transporteras flera av komponenterna som exempelvis elmotorerna från ungerska Györ med hjälp av tåg istället för lastbilar.
Fabriken i Györ är också helt koldioxidneutral och battericellsproducenten måste använda 100 procent förnyelsebar energi.
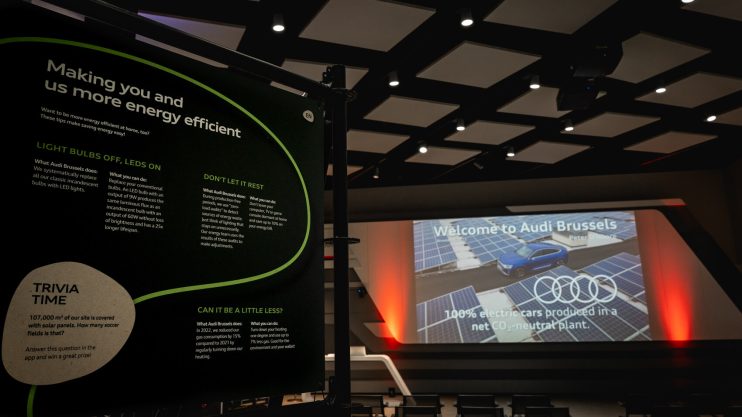
Vatten, bin, flora och fauna
När det gäller användandet av vatten har man också gjort omfattande framsteg och halverat användandet sedan 2015. Framförallt kommer besparingen från en ny förbehandlingslinje och ett återvinningssystem.
På ett liknande sätt återanvänder man mer vatten än tidigare när man testar så att bilarna är vattentäta. Här har man gått från att använda 16 liter istället för 110 som tidigare.
När det gäller tvättanläggningen för lastbilar och produktionsfordon har man gått från att använda 127 liter till enbart 16.
Audi i Bryssel jobbar också med att öka mängden bin på fabriksområdet eftersom det bidrar till spridandet av pollen. Man har även inventerat flora och fauna på fabriksområdet och arbetar aktivt med att motverka invasiva arter.

Världsledande i hållbarhet
Alla de här olika åtgärderna leder tillsammans fram till att Audi lyckades bli den första massproducerande bilfabriken i världen som är koldioxidneutral 2018. Men bara för att man lyckades åstadkomma det här stoppar inte hållbarhetsarbetet i Bryssel-fabriken.
Under nästa år siktar man även på att minimera användandet av vatten genom att använda sig av ett cirkulärt kretslopp för rening med hjälp av partnern Hydria. Det långsiktiga målet är att successivt minska energiförbrukningen med 3 procent årligen.
Miljön bryr sig som bekant inte om utsläppen kommer i produktions- eller brukandefasen. Om målet är att göra ett så miljömedvetet val som möjligt av bil bör man snegla på någon av Audis elbilar som tillverkas i Bryssel.
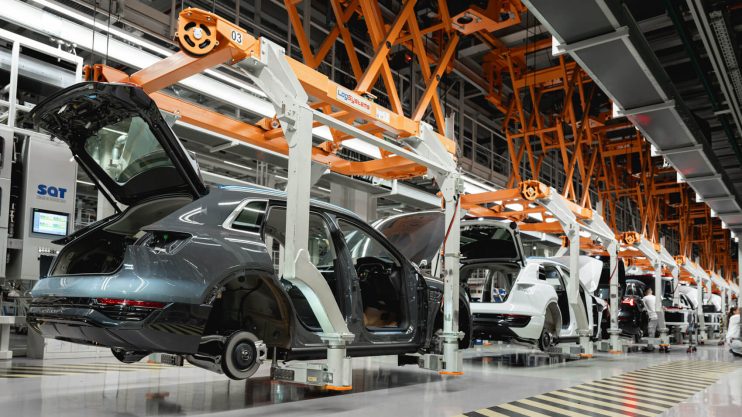